Manufacturing Growth
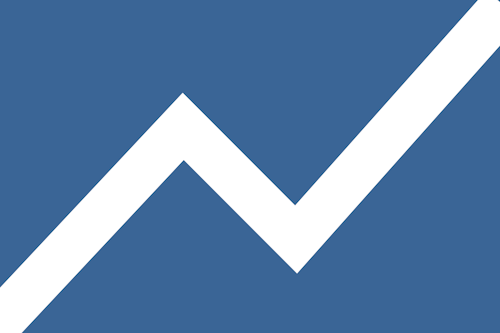
Advanced Manufacturing and the Future of the American Economy
The debate over manufacturing is stuck in a stale back and forth over whether traditional industries can, or should, be saved. But this debate misses a fundamental truth—manufacturing isn’t dying, it’s changing. The move to “advanced” manufacturing signals a new era for one of the most culturally and substantially significant sectors of our economy. This emerging era requires a new discussion about the role of manufacturing in America’s future prosperity and a fresh look at the need for pro-manufacturing policies.
Introduction
Old Arguments in a New Era
The debate over manufacturing in America is trapped in a time capsule, replete with images of workers engaged in strenuous manual labor or operating heavy machinery on a factory floor. This frame has led to the development of three camps that have come to dominate the debate on national manufacturing policy.
In one camp are the “Preservationists,” who view manufacturing as an anchor of solid, middle-class employment and as an economic touchstone. Members of this camp often have ties to “rust belt” regions where traditional manufacturing was once a linchpin of prosperity and has now fallen on hard times. They are deeply concerned about the negative impacts that globalization and changes in the sector have had on key industries. Out of a desire to counter these forces and preserve the middle-class jobs and communities that traditional manufacturing has sustained, they have at times supported trade barriers to protect domestic industries from growing global competition and the elimination of “offshoring” incentives in the tax code.
In another camp are the “Pollyannas,” who believe that a declining role for manufacturing in America’s economy is similar to the transition undergone by the agricultural sector, which a century ago employed 40% of the workforce yet now employs just 2%. To them, today’s decline in manufacturing employment is simply a natural outcome of the ongoing transition to a service-based economy. In their view, manufacturing has no greater inherent value than any other economic activity1 and the offshoring of manufacturing is the inevitable outcome of welfare-enhancing free trade.2 As such, there is no reason to adopt a proactive manufacturing policy that could impede natural economic process or forestall transition to higher-value activities in line with our nation’s comparative advantage.
A third group, the “Pessimists,” argue that, even if it wants to, America simply cannot compete in manufacturing because of cheap foreign labor and lower environmental and regulatory standards in the developing world. Indeed, according to a recent study, China surpassed the United States in 2010 as the world’s largest manufacturer, ending America’s 110-year dominance in manufacturing.3 Pessimists argue that this trend is destined to continue, and that the United States can do very little about it
“The reality is that manufacturing isn’t dying
—it’s changing.”
Each of these camps owns a piece of the truth. The Preservationists are right that manufacturing jobs are good jobs that offer higher than average pay. And their protectionist inclinations are a reaction to the reality that American manufacturing has seen better days. According to one recent report, manufacturing output declined in 15 of 19 sectors over the last decade. Over the same period the country lost 5.5 million manufacturing jobs—nearly one-third of the manufacturing workforce.4 At the same time, Pollyannas are right to note that as economies mature, the share of gross domestic product (GDP) accounted for by manufacturing typically declines. Likewise, Pessimists are right that in some labor-intensive industries, the United States simply will not be able to compete and some traditional manufacturing jobs may never return.
But, while the views of these camps are grounded in some fundamental truths, each of them also misses the underlying phenomenon that is driving these developments. The reality is that manufacturing isn’t dying—it’s changing. Even as manufacturing has undergone a relative decline, it has actually become more important to the health of the U.S. economy. The sector is transitioning from low-tech, labor-intensive industries toward a manufacturing sector that is technology-intensive, high-productivity, and at the heart of our nation’s innovation system. With a wide array of breakthroughs in technology, productivity, and management, a new manufacturing has taken hold.
This new, or “advanced,” manufacturing has several hallmarks that distinguish it from the low-skilled enterprise that still holds sway over popular conceptions of American manufacturing. Today’s modern factory is heavily reliant on technology that allows manufacturers to engage in more precise and increasingly productive work. For example, today’s American manufacturing activities are likely to resemble those in General Electric’s Greenville Airfoils Facility in Piedmont, South Carolina, where workers use computer-controlled equipment to burn hundreds of tiny cooling holes into jet engine turbine blades.5 The new manufacturing also focuses on newer, innovative industries like advanced medical devices, clean energy technologies, and pharmaceuticals.
The move to “advanced” manufacturing signals a new era for one of the most culturally and substantially significant sectors of our economy. This emerging era requires a new discussion about the role of manufacturing in America’s future prosperity and a fresh look at the need for pro-manufacturing policies.
The New Manufacturing
This Isn’t Your Father’s Factory Floor
The manufacturing sector has been in relative decline for some time. From 1957 to 2007, manufacturing’s share of U.S. GDP declined from 27% to less than 12%,6 though much of this trend reflects declining prices for manufactured goods.7 In 1969, manufacturing accounted for 26% of national employment but accounts for only about 9% today. It would be easy to look upon these trends as the death knell for American manufacturing.
However, despite these relative declines, manufacturing remains a sizeable contributor to our economy and directly employs over 11.5 million people.8 Paradoxically, even as manufacturing’s relative share of employment and GDP has decreased in recent decades, manufacturing has actually become even more important to sustaining American prosperity. Manufacturing is the most capital-intensive and productive sector of the economy, and it is key to developing and commercializing new technologies. Manufacturing also has the largest employment and output multipliers of any sector of the economy, creating many indirect jobs and making it a key catalyst of broad economic growth. Moreover, a healthy manufacturing sector is central to the United States’ ability to reduce its large and persistent trade deficit.
The changes in the employment, industrial focus, and workforce skills associated with the new manufacturing should be viewed as the growing pains that accompany any significant metamorphosis. The most recent evolution in manufacturing has resulted in key differences between advanced and traditional activities. These differences have profound implications for the role of manufacturing in our economy and the design of national policy toward manufacturing.
New manufacturing thrives on and drives innovation.
Manufacturing is a core component of the nation’s innovation ecosystem. Firms engaged in manufacturing re-invest a significant portion of revenues in research and development (R&D). Overall, the manufacturing sector comprises two-thirds9 of industry investment in R&D and employs nearly 64% of the country’s scientists and engineers.10 Manufacturers also have unique opportunities to apply new technologies for specialized functions and achieve economies of scale at the plant or firm,11 making the return on manufacturing R&D significant.
The transition to advanced manufacturing will enhance the sector’s role in fostering innovation and developing and commercializing new technologies. Advanced manufacturing industries, including semiconductors, computers, pharmaceuticals, clean energy technologies, and nanotechnology, play an outsized role in generating the new technologies, products, and processes that drive economic growth.
Advanced manufacturing is also characterized by the rapid transfer of science and technology into manufacturing processes and products, which in and of itself drives innovation. The research-to-manufacturing process is cyclical, with multiple feedbacks between basic R&D, pre-competitive research, prototyping, product development, and manufacturing. This opens new possibilities for product development and manufacturing.12
Because of the technological complexity of many modern, science-based industries, technology development often requires interactions among experts from many different disciplines. It is therefore supported by “geographic clustering” of related manufacturing, supply chain, research, and educational facilities.13 According to a 2004 report by President Bush’s Council of Advisors on Science and Technology (PCAST), “design, product development, and process evolution all benefit from proximity to manufacturing, so that new ideas can be tested and discussed with those working ‘on the ground.’”14
As a result, when a high-tech manufacturing cluster forms, it often attracts the co-location of R&D activities and helps sustain the global competitiveness of the entire region. This is why Intel recently decided to build a new state-of-the-art R&D facility near Portland, Oregon where it has long had a high-tech manufacturing presence, as well as related silicon manufacturers, suppliers, and a high-skilled workforce.15
In new manufacturing, comparative advantage is created, not endowed.
The conventional view is that a nation’s comparative advantage is determined by a set of static endowments such as land, labor, and capital. If a nation has an abundance of labor, the argument goes, it should specialize in labor-intensive production. The application of this outlook to traditional manufacturing would imply a comparative advantage for America’s lower-cost, labor-abundant competitors. Indeed, this assessment has led the Pollyannas and Pessimists to argue for a de-emphasis on manufacturing or to lament our nation’s inability to compete.
The high-productivity, technology-intensive nature of advanced manufacturing counters both the Pollyannas’ and Pessimists’ views about American manufacturing’s ability to compete. Today, as the result of the rapid evolution of technology and the mobility of financial capital, a nation’s comparative advantages are highly dynamic. In advanced manufacturing, such advantages are increasingly created, not endowed, and they are fundamentally shaped by public policy. Government policy helps to shape attractive environments for investment and provide key inputs like technological infrastructure, basic research funding, and a highly skilled workforce. Effective government policy can support efforts in the private sector to create competitive new processes and products, and can foster well-networked regional industry innovation clusters that sustain competitive advantage.
New manufacturing involves more than cheap labor.
In the era of new manufacturing, there are reasons to fundamentally revisit the conclusion that the United States cannot compete because of labor costs. In these industries, policy and productivity matter more than cheap labor. The Semiconductor Industry Association estimates that Chinese government policy, not low cost labor, is the major reason for a cost advantage of $1 billion over 10 years for building and operating a semiconductor plant in China rather than the United States. Nearly 70% of the cost difference is due to tax benefits and 20% to direct subsidies, with only 10% attributable to lower labor costs.16
Low labor costs also can’t explain why Germany, where hourly compensation costs in manufacturing sectors are nearly 30% higher than the United States, has maintained robust and highly competitive manufacturing industries.17 Nor does it explain how semiconductors, a capital-intensive, high-tech sector, are today largely manufactured in Asia and not in the United States. Labor costs can be important for simpler assembly operations, but the high up-front capital investments required to build new advanced manufacturing facilities and the high-productivity, high-skill processes employed in such factories make factors other than labor costs a much more important component of competitive advantage.18
As Dow Chemical CEO Andrew Liveris writes, “countries with higher wage rates can compete—and prevail—against countries with substantially lower wage rates, and that’s good news for America.”19 A recent study by the Boston Consulting Group helps to underscore the point.20 According to their analysis, China’s strengthening currency, wages that are rising by 17% per year, and a more flexible work environment are already helping to moderate the labor cost disparity. The group estimates that, when adjusted for superior U.S. productivity, China’s average wage was 31% of an American worker’s in 2010 and will soon close to 44% by 2015. Combine that with rising transportation and fuel costs, as well as higher quality in the United States, and it is perhaps not coincidental that companies like Caterpillar and Ford have announced a repatriation of some manufacturing operations.21
New manufacturing needs a new type of worker.
Modern, or “advanced,” manufacturing has made leaps and bounds in terms of technology and productivity. In turn, today’s manufacturing worker must possess a new set of skills. Instead of running a machine press or using hand tools, today’s manufacturing worker is likely to operate computer-controlled precision equipment to build advanced medical devices, make new drugs, or assemble wind turbines. This fundamental shift has created new opportunities for high-skilled employment and has profound implications for the U.S. manufacturing workforce.
New manufacturing workers must have a wide array of abilities including the production skills to set up and operate processes, design and development skills to continuously improve those processes, as well as proficiency in maintenance, repair and supply chain logistics.22 This shift is so substantial that it is creating significant change in the manufacturing workforce. In a 2009 survey of manufacturers, 51% indicated that, even during the height of the recession, they were experiencing worker shortages in skilled production areas. Concerns about skills shortages were particularly acute in leading industries such as aerospace and life sciences.23 This dynamic is playing out even in hard hit traditional manufacturing mainstays like Cleveland, Ohio, where makers of pharmaceuticals and aerospace equipment are struggling to find and hire workers with the aptitude and math and computer skills needed for the new manufacturing.24
Manufacturing and The Future U.S. Economy
Manufacturing Growth and Jobs
Advanced manufacturing is vital to widespread job creation and economic growth.
Manufacturing already has a major impact on American employment and prosperity. Manufacturing jobs are “good” jobs that pay higher-than-average wages. In March 2009, manufacturing companies paid $32 per hour in wages and benefits, while all employers paid an average of $29.39 per hour—a 9% wage premium.25
Beyond direct job creation, manufacturing generates high levels of output and employment throughout the economy. The sector has the largest “employment multiplier,” according to economist Josh Bivens, who finds that each job created in manufacturing leads to the creation of 2.91 additional jobs, compared to 1.54 jobs in business services and 0.88 jobs in retail trade.26 The manufacturing “output multiplier” is also higher than any other sector of the economy. Every dollar in final sales of manufacturing products supports $1.40 in output from other economic sectors. Most industries, including professional and business services have multipliers of less than $0.70, and no other industry has a multiplier above $1.10.27 As the demand for manufacturing grows, it therefore spurs investment, job creation, and innovation throughout the economy.28 Conversely, the erosion of U.S. manufacturing output and employment has an outsized and often devastating impact on regional economies.
The economic multiplier effects from manufacturing are even greater in high-tech, “advanced” manufacturing sectors. The Milken Institute finds that every job created in electronic computer manufacturing generates 15 other jobs throughout the economy.29 Intel’s new $4 billion R&D and manufacturing facility near Portland, Oregon, for example, will create 6,000 to 8,000 construction jobs and nearly 1,000 permanent high-tech jobs in the area. The government will benefit from property and sales taxes, and additional jobs will be created in downstream industries like home construction and services.30
In addition to creating jobs, manufacturing is a driver of widespread economic growth. As Federal Reserve Chairman Ben Bernanke notes, increasing productivity is “perhaps the single most important determinant of living standards” and prosperity.31 And as one of the most intensive users of capital equipment and technology in the economy, the manufacturing sector is one of the nation’s most productive sectors; from 1987-2008, labor productivity in the U.S. manufacturing sector grew by 103%, nearly double the rate of 56% for the private sector as a whole.32
The Kindle Conundrum
In 2007, engineers and designers at a Silicon Valley research facility called Lab 126 developed the Amazon Kindle, a product that has begun to revolutionize the way we read books, magazines, and newspapers. A key innovation in the product was electronic ink, which changes the appearance of the device’s screen without illuminating it, allowing the Kindle to simulate a printed page.
The team at Amazon was ready to get to work manufacturing the new product at scale. They partnered with a Massachusetts-based company called E-Ink, which was one of the only companies in the country capable of producing electronic ink devices. But E-Ink didn’t have the technology to produce the Kindle screen; Amazon needed to find a second partner.
The production technology needed to build the screen was similar to the technology used to build flat panel LCD screens, so Amazon needed a manufacturer with experience in that field. After scouring the United States for those kinds of capabilities, Amazon came up empty. As it turns out, LCD screens had ceased being produced in the United States in the mid-1990s even though the technology had been developed in America. As a result, Amazon was forced to look abroad, and contracted with a Taiwanese company with the capabilities to manufacture its device.
That’s not the end of the story, however. After the production of the Kindle commenced, the Taiwanese manufacturer, called Primeview, found that it could manufacture the Kindle even more cheaply if the creation of electronic ink for the device wasn’t located so far away from the manufacturing facility. As a result, Primeview purchased E-Ink and moved it—along with the entire U.S. electronic ink industry—to Taiwan. Because the United States lost capabilities to produce LCD flat panel displays, it lost out on producing one of the world’s leading e-readers, and ceded the emerging e-ink industry to foreign competitors. Today, when a U.S. consumer purchases a Kindle, it adds to the U.S. trade deficit.
Efforts to maintain the strength of advanced manufacturing will be key to ensuring that cutting-edge, next-generation technologies are developed in the United States. As an R&D-intensive endeavor, advanced manufacturing can create jobs and propel growth in previously unimagined ways. From 2001-2006 real output in U.S. manufacturing industries with higher than average R&D intensities grew substantially faster than their low-tech counterparts, with some low-tech industries experiencing absolute declines in real output.33 For instance, pharmaceuticals and medical equipment, with R&D intensities of 10% and 8% respectively, each expanded by nearly 39% over the period. By contrast, plastics and rubber (with a 2.3% R&D intensity) expanded by just 4.6% and electrical equipment (2.5% R&D intensity), actually declined absolutely by 6.3%.
It’s also important to note that even the innovative, high-tech services that Pollyannas point to as the future of the American economy will still depend on the maintenance of a vibrant U.S. manufacturing base. The manufacturing sector is the largest supplier of technologies for the high-tech service sector, and the effective integration of these technologies into service systems often requires close association with manufacturing firms as well the development of the technologies themselves. Given that manufacturing industries account for nearly 70% of industry R&D and nearly the same share of the country’s scientists and engineers, there’s no doubt that a diminished advanced manufacturing sector would negatively impact U.S. competitiveness in high-tech services.34
New manufacturing will help determine whether America leads or follows in the world economy.
In the post-World War II period, America has enjoyed an unparalleled status as the world’s economic leader. While we are still at the top of the international heap, globalization and technological development have allowed hungry new competitors like China, India, and Brazil to enter the scene and challenge America’s global position.
As much as the Preservationists would hope to insulate traditional manufacturing from the detrimental impacts of global competition, the genie is out of the bottle. We have no choice but to take on other nations in the contest for new markets and customers. Developing a robust advanced manufacturing sector will help make the difference between being a global leader or follower—a reality our rivals have already recognized and embraced.
Today, numerous countries are leveraging strategic government investments to move into advanced technology industries, challenging America’s historic leadership in the area. Many European and Asian nations view advanced manufacturing as a strategic industry because of its unique ability to add value to their economies—in the form of skilled jobs, new parts suppliers, services, tax revenues, expanded export opportunities, new spin-offs and innovations, and greater economic growth. As a result, these nations are pursuing intentional policy strategies to develop advanced manufacturing industries.
Many countries, including Germany, China, Japan, Singapore, Taiwan, and South Korea, offer incentives to high-tech firms to establish manufacturing facilities within their borders. These incentives include tax breaks, cash grants, free land, access to cheap credit, speedy regulatory approval, and the public provision of infrastructure and high-value human capital.35 For example:
- Germany supports its advanced manufacturing core, which largely produces specialized products for advanced technologies, with a robust network of government-funded research institutes that tackle applied research problems for manufacturers and help them adopt cutting edge technologies.36 Manufacturing still comprises 17% of GDP in Germany and the country runs a large trade surplus in manufactured goods.
- Japan is implementing a well-funded science and technology strategy that focuses on R&D and new manufacturing processes in priority areas like nanotechnology, energy, manufacturing technology, and IT, with government ministries working in close collaboration with industry.37 Manufacturing comprises 21% of the nation’s GDP and also contributes to a large and sustained trade surplus.
- China funds and promotes science-based industrial parks that include R&D centers that can be used by multiple companies. In their efforts to develop high-tech “Strategic Emerging Industries,” including next-generation information technology, biotechnology, and clean energy, the Chinese government also offers free land, low-cost financing, and money for R&D to companies that establish manufacturing facilities within their borders.38
- Taiwan offers free or discounted rent to companies that establish corporate headquarters in designated industrial districts. They also have a very generous combined tax credit for investments in R&D and new manufacturing equipment.39
- Singapore offers firms grants toward education and the training of engineers.40 In the emerging biomedical sector, the Singaporean government has also made major commitments to invest in R&D, while public research institutes collaborate with industry to perform cutting-edge research and boost manufacturing capabilities.41
Over the past 20 years, the rate of growth in world gross revenue from high-technology manufacturing industries has grown at double the rate of other manufacturing industries, suggesting that many nations are successfully climbing the value-added ladder to a high-tech economy.42
Without a commitment to developing its own advanced manufacturing base, America will quickly find itself unable to keep up with the competition. In an ominous development, the Silicon Valley-based firm Applied Materials, the world’s leading manufacturing of equipment used to make solar cells, recently constructed the world’s largest private solar R&D facility in China to locate near the nation’s fast-growing solar manufacturing hubs.43 IBM, GE, and Dow Chemical have all recently opened new R&D facilities abroad, and recent research confirms that the more a company offshores manufacturing, the more it offshores new product development and engineering.44 Indeed, from 1999-2007, U.S.-based manufacturing firms’ investment in R&D outside of the United States grew at nearly three times the rate of domestic R&D investment.45
The United States is also lagging behind its competitors in developing advanced manufacturing capabilities in a number of strategic growth industries. For instance, the United States currently lags behind other nations in the production of virtually all clean energy technologies, and is behind China and Germany in attracting investment into the sector.46 In the semiconductor industry, the percentage of global semiconductor production located in the United States fell to 14% in 2009, down from 25% in 2005, while China, Taiwan, and South Korea increased their shares.47
Because of the increasing co-location of manufacturing and R&D, losing advanced manufacturing capabilities in one industry can lead a nation to be locked-out of future technologies that spring from or depend upon that industry. In the 1980s, U.S. companies began offshoring the assembly of printed circuit boards—key components of electronics and personal computers—to China, South Korea, and Taiwan. Eventually, as companies in those countries became more sophisticated at production, they began to seek higher-value work—first moving into complete product assembly and then eventually design. Today, virtually all Windows notebook PCs are produced and designed in Asia.48
Batteries offer another cautionary parable. As former Intel CEO Andy Grove has written, the United States lost its lead in batteries 30 years ago when it abandoned consumer electronic devices and the supply chains that comprised the industry’s manufacturing base. “Whoever made batteries then gained the exposure and relationships needed to learn to supply batteries for the more demanding laptop PC market, and after that, for the even more demanding automobile market,” writes Grove. “U.S. companies did not participate in the first phase and consequently were not in the running for all that followed.”49
U.S. firms abandoned the rechargeable lithium-ion battery market in the early 1990’s when it was merely a $100 million industry. Today, the advanced battery market has grown one-hundred-fold to become a more than $10 billion sector. Having long-ago ceded leadership in advanced batteries, America watched the incredible dividends associated with this fast-growing sector accrue primarily to international competitors.50 As detailed in one of the spotlight sections of this report, even the lithium-ion batteries used in Chevy’s much anticipated electric car, the Volt, are supplied by South Korean battery manufacturer LG Chemical.
America can remain a manufacturing leader—if the nation dedicates the resources and investment necessary to capitalize on its sizeable advantages. That means moving on from focusing on what manufacturing used to be to developing policies to support new manufacturing in the 21st century economy.
Battery Power
General Motors, the signature American car company, recently rolled out its new electric vehicle, the Chevy Volt, which it hopes will help revive its image and revitalize sales. While GM hopes the Volt will become a symbol of American ingenuity, what’s under the hood tells a different story. The lithium-ion batteries used to power the Volt—which are the highest value-added component in the car—are actually developed and manufactured by South Korean battery maker LG Chemical.
GM was forced to go abroad because of a dearth of advanced battery manufacturing capacity in the United States. How is it that the United States is not competitive in producing advanced battery technology for which there is such a large and growing global demand? It turns out that U.S. capacity to manufacture rechargeable batteries left the country long ago, when the locus of consumer electronics manufacturing shifted to Asia. Much of the innovation in battery technology occurred in the consumer electronics market, as consumers demanded more and more power from smaller components. And after the consumer electronics manufacturing industry settled in Asia, research and development into batteries followed.
Much of the world’s consumer electronics industry sprouted up in Japan and South Korea, which also had strong auto industries, and were the first to push into hybrid vehicles that utilized advanced battery technology. As a result of their first-mover advantages in advanced battery technology, these nations’ companies are better positioned to reap the economic rewards of the recent move toward vehicle electrification in the developed world and the large economic opportunities associated with this fast-growing segment of the advanced battery market. The United States abandoned the lithium-ion battery market when it was worth only a few hundred million dollars; today, it’s more than $10 billion.51
New manufacturing will help America sell to the world and cut our trade deficit.
As the world economy continues to grow, 2 billion new middle-class consumers are set to enter the market—outside our borders. To remain a prosperous nation, we must resist the Preservationist temptation to turn inward as well as the Pessimist prescription to write manufacturing off as more suited for other nations. Instead, we need to ensure American manufacturing has a robust presence in global trade and remains capable of selling to these new customers.
Over the last three decades, the United States has generated a positive and growing balance of trade in services, but a significant and worsening trade deficit in goods. In 2006, the nation’s overall trade deficit reached a record $760 billion. As the ensuing recession drove a sharp drop in imports, the trade deficit has fallen in recent years.52 Yet in 2010, it still stood at nearly $500 billion, as a $647 billion deficit in goods53 completely erased a comparatively modest $149 billion trade surplus in services. Many argue that a persistent trade deficit of this magnitude is a drag on economic growth and represents a hidden tax on future generations.54
If America wishes to close its trade deficit through means other than a deep recession or much lower consumption, the country must greatly increase its exports of manufactured goods. While the growing trade in services is clearly a significant and welcome benefit for the United States, it alone is not large enough to close the trade deficit. This is because the large majority of U.S. trade—nearly 70% of exports and 83% of imports—is still in goods. Manufactured goods in particular comprise 57% of U.S. exports.55
It took 11 years for service exports to double from $268 billion in 1999 to $543 billion in 2010. Even when assuming zero growth in services imports (which stood at $394 billion in 2010), the current positive balance in services would need to quadruple to eliminate the deficit in manufactured goods.56 In a world where the Internet has made service jobs more “tradeable,” international competition in these sectors is mounting, and it is far from a slam-dunk to count on the growth of services to restore America’s trade balance on its own.57 As such, America’s future in a globalized economy still remains inextricably tied to a new era of manufacturing exports.
Rebuilding A National Manufacturing Policy
New Ideas for New Manufacturing
To take advantage of the opportunities presented by the new era of advanced manufacturing and to avoid falling behind our competitors, America needs to take action. Government must play a role by implementing a series of reinforcing policies to address the business, labor, and financial challenges that create obstacles for advanced manufacturers. Potential solutions and areas for exploration should include:
Bonus Manufacturing Tax Credit
Offer a bonus R&D credit to companies that also manufacture 50% or more of their products in the U.S. The bonus credit would be on a sliding scale, based on the share of the company’s total manufacturing output that is produced domestically.
Building an Advanced Manufacturing Workforce
A new, national emphasis is needed across the educational continuum to provide individuals with the skills they need to succeed in advanced manufacturing. This includes an emphasis on developing science, technology, math, and engineering skills at the K-12 level, providing incentives for companies to make on the job training available for workers interested in improving their skill sets, creating a culture of continuous learning that allows mid-career workers to quickly course-correct and acquire new skills, and closer coordination between employers and local educational institutions to create an employee pipeline.
Create “Manufacture America Bonds” Program
Similar to the widely successful “Build America Bonds” program,58 which lowers infrastructure-related borrowing costs for state and local governments, the federal government could create a new financing tool to reduce borrowing costs for state and municipal governments to support private investment in advanced manufacturing activities. The federal government would pay a direct subsidy to state or municipal bond issuers equal to 35% of the interest costs on taxable bonds. State financing entities could then lend capital at lower interest rates to advanced manufacturing firms to open new manufacturing facilities or retool existing ones. This would reduce the net borrowing costs for manufacturers and leverage greater private sector investment in advanced manufacturing.
Expand the Manufacturing Extension Partnership
Small and medium-sized manufacturers often lack the resources to stay informed about the latest cutting-edge developments in manufacturing technology and suffer a competitive disadvantage as a result. To support America’s advanced manufacturers, Congress should increase funding for the Department of Commerce’s Hollings Manufacturing Extension Partnership (MEP), which provides technical assistance to help small and medium-sized American manufacturers adopt new technologies and improve productivity.59
Advanced Manufacturing Zones
Create community-based investment zones (based on the Empowerment Zone concept) dedicated to advanced manufacturing. These zones would have access to special tax incentives to help jumpstart the nation’s advanced manufacturing base while creating new centers of business innovation.60
Continue to Implement the Advanced Manufacturing Partnership
The Administration has adopted a cross-departmental effort to promote advanced manufacturing through support for research and development of new technologies and methods, development of design methodologies that reduce time and obstacles to market deployment, establishment of shared infrastructure for small manufacturers, and other initiatives. This initiative should be fully and aggressively implemented for long-term results.61
Advanced Manufacturing Technology Consortia
Support a new, public-private effort led by the Department of Commerce’s National Institutes of Standards and Technology (NIST) to fund industry-led manufacturing research collaborations to speed the development and commercialization of new manufacturing technologies. This program, which will be implemented later this year, will fund public-private consortia to perform pre-competitive R&D, create the infrastructure necessary for more efficient transfer of technology, and eliminate barriers to innovation, all of which will enhance U.S. manufacturing competitiveness and spur economic growth.62
Advanced Manufacturing Revolving Loan Fund
Provide capitalization for state-managed revolving loan funds that provide low-cost financing for the retooling or expansion of advanced manufacturing facilities and the adoption of innovative manufacturing process technologies. To effectively leverage federal funds, states could provide one dollar of their own funding for every dollar of federal funds.63
Investment Tax Credit for Machinery and Equipment
Implement a federal investment tax credit (ITC) to boost capital investment in the economy. The ITC could be targeted toward investments that have the largest economic returns, such as industrial machinery. Reducing the after-tax cost of capital equipment would encourage greater investment in manufacturing equipment, which boosts productivity and economic growth.64
Conclusion
Unleashing New Manufacturing
Advanced manufacturing is critical for the future prosperity of the U.S. economy. Not only does it have the potential to generate and sustain many jobs throughout the economy, but it is a key source of innovation, productivity gains, and exports. A robust advanced manufacturing sector is also a prerequisite for developing new technologies that will form the basis for tomorrow’s innovative growth industries.
While U.S. manufacturing has rebounded somewhat since the Great Recession, the strength of its recovery has dwindled and the long-term outlook is unclear.65 But this welcome momentum should not be taken for granted. As our economic competitors continue to target strategic high-tech manufacturing industries and as billions of new middle-class consumers enter the global economy in the coming decades, the United States must rise to the challenge. The time has come to reaffirm the importance of advanced manufacturing to America’s long-term economic prosperity and to unleash the era of new manufacturing.
Endnotes
For example, according to George Mason University Economist Donald Boudreaux, “The value of a dollar’s worth of cloth is the same as a dollar’s worth of web design—one dollar.” See Steve Fritzinger, “Factories in decline? It’s OK, services will do nicely,” BBC News, March 17, 2011. Accessed September 23, 2011. Available at: http://www.bbc.co.uk/news/world-us-canada-12774290. Columbia University economist Jagdish Bhagwati, goes so far as to label supporters of manufacturing fetishists. See Jagdish Bhagwati, “The Manufacturing Fallacy,” Op-ed, Project Syndicate, August 27, 2010. Accessed September 1, 2011. Available at: http://www.project-syndicate.org/commentary/bhagwati3/English.
In 2004, N. Gregory Mankiw, former Chairman of President George W. Bush’s Council of Economic Advisors, encapsulated this view when he told an audience that, “I think outsourcing is a growing phenomenon, but it’s something that we should realize is probably a plus for the economy in the long run. We don’t have a comparative advantage in producing clothing, textiles, and that’s one of the reasons we’ve tended to lose textile jobs. Maybe we’ve learned that we don’t have a comparative advantage in radiologists.” Edmund L. Andrews, “Democrats Criticize Bush Over Job Exports,” The New York Times, February 11, 2004. Accessed September 27, 2011. Available at: http://www.nytimes.com/2004/02/11/us/democrats-criticize-bush-over-job-exports.html. See also Jonathan Weisman, “Bush Report Offers Positive Outlook on Jobs,” The Washington Post, February 10, 2004. Accessed September 27, 2011. Available at http://www.washingtonpost.com/ac2/wp-dyn/A26982-2004Feb9?language=printer.
Peter Marsh, “US manufacturing crown slips,” Financial Times, June 20, 2010. Accessed September 1, 2011. Available at: http://www.ft.com/intl/cms/s/0/af2219cc-7c86-11df-8b74-00144feabdc0.html#axzz1Q1VsIsNf.
Stephen J. Ezell and Robert D. Atkinson, “The Case for a National Manufacturing Strategy,” Report, The Information Technology and Innovation Foundation, April 2011. Accessed September 1, 2011. Available at: http://www.itif.org/publications/case-national-manufacturing-strategy.
Peter Coy, “The Case for Making it In America,” Bloomberg Businessweek, May 5, 2011. Accessed September 1, 2011. Available at: http://www.businessweek.com/magazine/content/11_20/b4228011719321.htm.
Gregory Tassey, “Rationales and Mechanisms for Revitalizing U.S. Manufacturing R&D Strategies,” Strategy Paper, Journal of Technology Transfer, January 29, 2010, p.7. Accessed September 23, 2011. Available at: www.nist.gov/director/planning/upload/manufacturing_strategy_paper.pdf.
United States, Department of Commerce, National Institute of Standards and Technology, “The Facts about Modern Manufacturing,” Report, The Manufacturing Institute, 2009, 8th Ed., p.11. Available at: www.nist.gov/mep/upload/FINAL_NAM_REPORT_PAGES.pdf.
United States, Department of Labor, Bureau of Labor Statistics, “Manufacturing: NAICS 31-33,” Industries at a Glance, Accessed September 1, 2011. Available at: http://www.bls.gov/iag/tgs/iag31-33.htm#workforce.
United States, Department of Commerce, National Institute of Standards and Technology, “The Future of the Hollings Manufacturing Extension Partnership,” Report, December 2008. Accessed September 1, 2011. Available at: http://www.nist.gov/mep/upload/MEP_ExecSummary72dpi.pdf.
Raymond Wolfe, “U.S. Business R&D expenditures increase in 2007; Small Companies Perform 19 percent of Nation’s Business R&D,” InfoBrief, National Science Foundation, July 2009, NSF 09-316. Accessed September 23, 2011. Available at: http://www.nsf.gov/statistics/infbrief/nsf09316/nsf09316.pdf.
United States, Department of Commerce, Economics & Statistics Administration, “Engines of Growth: Manufacturing Industries in the U.S. Economy,” Report, 1995. Accessed on September 1, 2011. Available at: http://www.esa.doc.gov/Reports/engines-growth-manufacturing-industries-us-economy-0.
United States, Executive Office of the President, President’s Council of Advisors on Science and Technology, “Sustaining the Nation’s Innovation Ecosystems: Report on Information Technology Manufacturing and Competitiveness,” Report, January 2004. Accessed September 23, 2011. Available at: http://www.whitehouse.gov/sites/default/files/microsites/ostp/pcast-04-itreport.pdf.
Karen G. Mills, Elisabeth B. Reynolds, and Andrew Reamer, “Clusters and Competitiveness: A New Federal Role for Stimulating Regional Economies,” Policy Brief, Brookings Institution, April 2008. Accessed September 1, 2011. Available at: www.brookings.edu/papers/2008/04_competitiveness_mills.aspx. See also Tassey, p. 7.
United States, Executive Office of the President, President’s Council of Advisors on Science and Technology, “Sustaining the Nation’s Innovation Ecosystems: Report on Information Technology Manufacturing and Competitiveness.”
John Mulqueen, “Intel Pops the Cork: Oregon and Arizona Welcome Huge New R&D and Manufacturing Investments,” Site Selection, November 2010. Accessed September 1, 2011. Available at: http://www.siteselection.com/ssinsider/bbdeal/Intel-Pops-the-Cork.cfm.
United States, Congress, U.S. China Economic and Security Review Commission, “China’s High- Technology Development,” Statement by George Scalise, April 21, 2005. Accessed September 2, 2011. Available at: http://www.uscc.gov/hearings/2005hearings/written_testimonies/05_21_22wrts/scalise_george_wrts.htm.
United States, Department of Labor, Bureau of Labor Statistics, Elizabeth Zamora and Jacob Kirchmer, “Compensation Costs in Manufacturing Across Industries and Countries, 1975-2007,” Monthly Labor Review, June 2010. Accessed September 2, 2011. Available at: http://www.bls.gov/opub/mlr/2010/06/art3full.pdf.
United States, Executive Office of the President, President’s Council of Advisors on Science and Technology, “Sustaining the Nation’s Innovation Ecosystems: Report on Information Technology Manufacturing and Competitiveness.”
Andrew Liveris, Make it in America: the Case for Reinventing the Economy, John Wiley and Sons Inc., Hoboken, NJ, 2011, p.61, Print.
“Made in the USA, Again: Manufacturing Is Expected to Return to America as China’s Rising Labor Costs Erase Most Savings From Offshoring,” Press Release, Boston Consulting Group, May 5, 2011. Accessed September 2, 2011. Available at: http://www.bcg.com/media/PressReleaseDetails.aspx?id=tcm:12-75973.
Coy.
United States, Department of Labor, “High Growth Industry Profile: Advanced Manufacturing,” Accessed September 2, 2011. Available at: http://www.doleta.gov/brg/indprof/Manufacturing_profile.cfm.
“People and Profitability: A Time for Change – A 2009 People Management Practices Survey of the Manufacturing Industry,” Deloitte Consulting LLP, Oracle, and the Manufacturing Institute, February 19, 2010. Accessed September 2, 2011. Available at: http://institute.nam.org/view/2001005064765286263/info.
Motoko Rich, “Factory Jobs Return, but Employers Find Skills Shortage,” The New York Times, July 1, 2010. Accessed September 2, 2011. Available at: http://www.nytimes.com/2010/07/02/business/economy/02manufacturing.html.
“The Facts about Modern Manufacturing,” p. 11.
Josh Bivens, “Updated Employment Multipliers for the U.S. Economy,” Report, Economic Policy Institute, August 2003. Accessed September 2, 2011. Available at: http://www.epi.org/page/-/old/workingpapers/epi_wp_268.pdf.
“The Facts about Modern Manufacturing,” p. 11.
“The Facts about Modern Manufacturing,” p. 11.
Ross C. Devol, Perry Wong, Armen Bedroussian, Candice Flor Hynek and David Rice, “Manufacturing 2.0: A More Prosperous California,” Report, Milken Institute, June 2009. Accessed September 2, 2011. Available at: http://www.milkeninstitute.org/publications/publications.taf?function=detail&ID=38801202&cat=resrep.
John Mulqueen, “Intel Pops the Cork: Oregon and Arizona Welcome Huge New R&D and Manufacturing Investments.”
Ben S. Bernanke, Speech, Massachusetts Institute of Technology 2006 Commencement, Massachusetts Institute of Technology, Cambridge, Massachusetts, June 9, 2006. Accessed September 2, 2011. Available at: http://www.federalreserve.gov/newsevents/speech/bernanke20060609a.htm.
“The Facts about Modern Manufacturing,” p. 28.
R&D intensity is defined by R&D spending divided by GDP for the entire economy and R&D spending divided by sales for companies, industries, or sectors. See Tassey, p. 12.
R&D intensity is defined by R&D spending divided by GDP for the entire economy and R&D spending divided by sales for companies, industries, or sectors. See Tassey, p. 7.
Pete Engardio, “Can the Future Be Built in the America?” Bloomberg Businessweek, September 10, 2009. Accessed September 2, 2011. Available at: http://www.businessweek.com/magazine/content/09_38/b4147046115750.htm.
For instance, Germany’s Fraunhofer Institutes offer a national network of research centers that collaborate with private industry to perform cutting edge applied research to promote economic welfare and achieve other goals important to society at large. See: http://www.fraunhofer.de/en/about-fraunhofer/mission/.
United States, Department of Commerce, International Trade Administration, Jane Corwin and Rebecca Pucket, “Japan’s Manufacturing Competitiveness Strategy: Challenges for Japan, Opportunities for the United States,” April 2009. Accessed September 2, 2011. Available at: http://www.trade.gov/mas/ian/build/groups/public/@tg_ian/documents/webcontent/tg_ian_002085.pdf.
Robert D. Atkinson et al, “Rising Tigers, Sleeping Giant,” Breakthrough Institute and Information Technology and Innovation Foundation, November 2009. Accessed September 2, 2011. Available at: http://thebreakthrough.org/blog/2009/11/rising_tigers_sleeping_giant_o.shtml.
United States, Executive office of the President, President’s Council of Advisors on Science and Technology, “Sustaining the Nation’s Innovation Ecosystems: Report on Information Technology and Competitiveness.”
United States, Executive office of the President, President’s Council of Advisors on Science and Technology, “Sustaining the Nation’s Innovation Ecosystems: Report on Information Technology and Competitiveness, p. 12.
Lim Chuan Poh, “Singapore Betting on Biomedical Science,” Issues in Science and Technology, Spring 2010. Accessed September 2, 2011. Available at: http://www.issues.org/26.3/poh.html.
“Science and Engineering Indicators of 2008,” Report, National Science Foundation, pp. 6-4. Accessed September 2, 2011. Available at: http://www.nsf.gov/statistics/seind08/c0/c0i.htm.
Katherine Bourzac, “Applied Materials Moves Solar Expertise to China,” Technology Review, December 22, 2009. Accessed September 2, 2011. Available at: http://www.technologyreview.com/article/24274/.
Alan S. Brown, “Why Engineering is Moving Offshore,” Mechanical Engineering Magazine. Accessed September 2, 2011. Available at: http://memagazine.asme.org/web/Moving_Offshore.cfm.
Tassey, p. 5.
Robert D. Atkinson et al, “Rising Tigers, Sleeping Giant,” See also, “Who’s Winning the Clean Energy Race? 2010 Edition,” Pew Environment Group, March 29, 2011. Accessed September 2, 2011. Available at: http://www.pewenvironment.org/news-room/compilations/whos-winning-the-clean-energy-race-2010-edition-329349.
Richard McCormack, “U.S. Becomes a Bit Player in Global Semiconductor Industry,” Manufacturing and Technology News, February 12, 2010. Accessed September 2, 2011. Available at: http://www.manufacturingnews.com/news/10/0212/semiconductors.html.
Gary P. Pisano and Willy C. Shih, “Restoring American Competitiveness,” Harvard Business Review, July/August 2009. Accessed September 2, 2011. Available at: http://hbr.org/2009/07/restoring-american-competitiveness/ar/1.
Andy Grove, “How America Can Create Jobs,” Bloomberg Businessweek, July 1, 2010. Accessed September 2, 2011. Available at: http://www.businessweek.com/magazine/content/10_28/b4186048358596.htm.
Matthew Eisler, “Energy Innovation at Nanoscale: Case Study of an Emergent Industry,” May 23, 2011. Accessed September 23, 2011. Available at: http://www.scienceprogress.org/2011/05/innovation-case-study-nanotechnology-and-clean-energy/.
Grove, “How to Make an American Job.” See also Pisano and Shih, “Restoring American Competitiveness.”
Floyd Norris, “Recession’s Silver Lining: U.S. Trade Deficit is Down the Most on Record,” The New York Times, February 12, 2010. Accessed September 2, 2011. Available at: http://www.nytimes.com/2010/02/13/business/economy/13charts.html.
Of this $647 billion, it worth noting that $265 billion is attributable to petroleum imports.
Ezell and Atkinson, “The Case for a National Manufacturing Strategy.”
United States, Census Bureau, “U.S. International Trade Data,” Accessed September 2, 2011. Available at: http://www.census.gov/foreign-trade/data/index.html.
Author’s calculation. United States, Census Bureau, “U.S. Trade in Goods and Services - Balance of Payments (BOP) Basis,” June 9, 2011. Accessed September 2, 2011. Available at: http://www.census.gov/foreign-trade/statistics/historical/gands.txt.
Tassey, p. 7.
United States, Department of the Treasury, “Build America Bonds,” May 16, 2011. Accessed on October 24, 2011. Available at: http://www.treasury.gov/initiatives/recovery/Pages/babs.aspx.
For more about the Manufacturing Extension Partnership, see United States, Department of Commerce, National Institute of Standards and Technology, “The Future of the Hollings Manufacturing Extension Partnership.”
For more about Advanced Manufacturing Zones, see Josh Freed and Mark Sagat, “Clean Energy Business Zones,” Idea Brief, Third Way, October 2009. Available at: http://www.thirdway.org/publications/195.
The Advanced Manufacturing Partnership (AMP) was originally proposed by the President’s Council of Advisors on Science and Technology, and was announced by President Obama in June of 2011. For more information on the AMP, see United States, Executive Office of the President, Office of the Press Secretary, “President Obama Launches Advanced Manufacturing Partnership,” Press Release, June 24, 2011. Accessed September 2, 2011. Available at: http://www.whitehouse.gov/the-press-office/2011/06/24/president-obama-launches-advanced-manufacturing-partnership. For the original recommendation by PCAST see: “Report to the President On Ensuring American Leadership in Advanced Manufacturing.”
For more information about the Advanced Manufacturing Technology Consortia program, see United States, Department of Commerce, National Institute of Standard and Technology, “Obama Administration’s Budget Request for NIST Includes Critical Science and Technology Investments to Advance U.S. Innovation and Boost Economic Recovery,” February 14, 2011. Accessed September 2, 2011. Available at: http://www.nist.gov/public_affairs/releases/budget_2012.cfm.
A similar proposal for clean energy manufacturing was introduced in the last Congress by introduced by Senator Sherrod Brown (D-OH). The Investments for Manufacturing Progress and Clean Technology (IMPACT) Act, would authorize the creation of a revolving loan fund valued at $30 billion. For bill text and background information, see: http://thomas.loc.gov/cgi-bin/bdquery/z?d111:s.01617:.
For a full explanation of the benefits of a federal Investment Tax Credit for machinery and equipment, see Matthew Stepp and Robert D. Atkinson, “An Innovation Carbon Price: Spurring Clean Energy Innovation while Advancing U.S. Competitiveness,” Information Technology and Innovation Foundation, March 30, 2011. Accessed September 27, 2011. Available at: http://www.itif.org/publications/innovation-carbon-price-spurring-clean-energy-innovation-while-advancing-us-competitive.
Suzy Khimm, “Will Washington Try to Fix the Manufacturing Crisis?” The Washington Post, September 15, 2011. Accessed September 16, 2011. Available at: http://www.washingtonpost.com/blogs/ezra-klein/post/will-washington-try-to-fix-the-manufacturing-crisis/2011/09/15/gIQAR2oEVK_blog.html?wprss=ezra-klein.